Monthly themes for leaders in manufacturing [Roadmap 2022]
Leaders in manufacturing:
A Roadmap to Engage Your Team
To help leaders in manufacturing, we put together a calendar!
What type of manufacturing leader would you like to be this year?
Similarly, what kind of team would you like to have?
Don’t just dream it.
Plan it.
New year, new beginnings!
This year has been challenging for leaders in manufacturing.
Consequently, next year like any year will feature its ups and downs too for your business.
The one constant? As a leader, you harvest what you sow.
Being a good manufacturing manager and making sure your employees are happy and productive at work is an ongoing effort.
To sum up, it comes down to regularly listening and tuning in with your team. Good leadership practice is to carve out time in your calendar upfront. That increases the chance of taking ACTION.
And actions are what build employee satisfaction.
Let’s start off on the right foot!
Plan the plan
Here we go:
- Stop the first 5 random people you bump into after reading this. What would they say you should focus on in 2021?
- Sit down with a focus group. Ask coworkers to think about the group when answering. Not themselves. What would people like to change, or to happen, next year?
- If you have a wellbeing council already, use their insights to get feedback and be inclusive. What works in your company culture?
- Get line managers to talk with their teams and send ideas and comments.
Next, decide on the final plan together with your leaders at all levels.
Prefer Word? You got it.
Wanna make it a bit catchy?
Go for…
A monthly theme!
Many leaders in manufacturing already have captivating names for company events.
For instance, Unilever’s Repair Week, or Koch’s surprise Popcorn Day.
What goals and objectives do you have as a business for the upcoming year? Plan activities and themes around these.
I.e. if your main goal is quality, plan for hands-on actions to improve this KPI.
In the same way that you defined what good quality is at your manufacturing site, define what your workforce thinks is a good celebration.
For example, when you reach a goal. Is it a monetary reward? A Waffle Friday party?
You can also extend the quality concept to the personal. What is ‘quality’ when it comes to mental health?
Or follow up Repair Week with a Repair-Your-Mind event to focus on how to reduce stress.
Here’s an example of a manufacturers monthly roadmap:
January: Lunch Roulette
As simple as it may seem, good workplaces need a strong social fabric.
How well do you know your teammates?
Help your colleagues break the ice by organizing a Lunch Roulette.
What happens when you mix people that normally don’t have lunch together?
Get to know another side of your colleagues over some food.
A simple way to strengthen social connections between colleagues, hands-on.
Employees sign up to go for lunch with a random coworker they normally don’t have lunch with.
In short, it’s a chance to get to know new colleagues.
Discover things that normally wouldn’t come up in the day-to-day, and have some fun!
How does it work?
1. Employees volunteer to go for lunch with a random colleague
2. The company pays for lunch (you’ll get more participants and the investment is small).
3. Next, use your Team Board to visualize who is lunching with who.
4. Afterwards, employees share their experience with the rest. Use daily huddles for people to quickly mention something they learned about the other.
“I didn’t know Jack plays in a band!”. Use post-it notes and hang them next to the photo of the coworker.
Free Lunch Roulette Starter Kit.
February: Conversations
Now that the team has started bonding a bit, it’s time for the line managers to step up.
For some managers, even a seemingly innocent question like “How are you doing lately?” can seem like a big step to ask.
There are many leadership styles in the manufacturing industry.
Subsequently, way too many line managers bark out orders and tell their employees what to do. Yet when it comes to psychosocial aspects of work, they freeze.
- Related: Nice leadership skills examples from the Vita Group
Many countries are stepping up to protect workers’ health and safety from a legal point of view. Particularly regarding psychosocial aspects.
Successful lean leaders in manufacturing use daily huddles and weekly meetings.
This way you can start the conversations about how your people are feeling on your shop-floor.
At companies using a device like the Celpax to measure the impact of your leadership actions, you can use the green-red concept as an ice breaker.
Keep it neutral by asking “What makes us press the green button on our team?”.
Then, start a simple list where you write the things that your people like at work (green button) and plan to make more of these.
Once you’ve established trust, continue with the areas where people would like to improve (red button).
More tips on how to start conversations.
March: Wellbeing Month
Working 12-hour shifts has a proven downside in health terms.
The same goes for rotating shifts and enduring unpredictable work schedules as recent research shows.
Perhaps nothing can be done about the shifts. But you sure can do a lot when it comes to planning the work schedules for your people. Unpredictable and last-minute changes mean it’s hard to attract and retain your best workers.
Even small things like picking up your kids or booking a doctor’s appointment become big hurdles.
In February you opened up the conversations around how people feel at work. Now it’s time to start acting.
To sum up, how can you promote healthy habits and support your manufacturing workers?
For example, as a scheduling compromise, perhaps nailing the schedule two weeks in advance is acceptable?
Would blue light blocking sunglasses for the morning drive home be appreciated?
What else can be done for work not to interfere so much with your people’s personal life? And reduce stress levels?
Is there a growing demand for on-site child care that would make you an attractive employer in your area?
Part-time jobs?
Flex?
Or other benefits that better reflect your workers’ needs?
Organize Healthy Snack Days during March. Let the conversations flow during daily huddles, weekly meetings and lunch breaks.
Bring in a masseur, or give vouchers for a local healthy meal. Got an extra budget? Cooking classes or on-site meals rock.
With baseline measurements, you can also verify the impact of your wellbeing program.
April: Upskill
The skills gap in manufacturing is a growing pain. Upskilling is a cheap way to attract new manufacturing workers. And hey, to keep your current talent.
Good leaders in manufacturing make sure that training is an ongoing theme in their business.
Firstly, what is most urgent? What would they appreciate the most?
Secondly, what needs to be done by law when it comes to health and safety training?
Remember your contractors, hourly workers, and self-employed. Talent can be found in many places. Involve your health and safety representatives early on.
Perhaps they can learn management and leadership skills online?
Upskilling improves your productivity and opens up promotion opportunities. It’s also good for morale. Lastly, personal growth is a great way to maintain a culture of continuous improvement.
Get your leadership team to reflect on how you identify future leaders in manufacturing.
Both future leaders at your company, but also within your industry.
May: Mental Health & Hot-Dog Day
Mental health is still a taboo topic at many worksites.
What can we do to change this?
A report ranked manufacturing as the 4th highest industry where workers suffer from anxiety or depression. It was a whopping 36% above the US average.
Start with giving your line managers training. Help them to properly address employees who are struggling with mental health issues.
It doesn’t matter if it’s personal or job-related. Both will impact their job performance.
- Related: Emotions in the workplace, “we hire the whole person”
Next, invite your workers for a Hot-Dog day. A great moment to start the conversations around anxiety and mental health.
Bring a speaker and hand out flyers with tips and advice. Above all, let them know where they can get individual help.
Anxiety, suicide thoughts, and stress… what can you do?
What tools are you offering?
Can your employees take mental health days for example? Is it “safe” to openly talk about these topics? Or do they feel it impacts their job security?
To sum up, men are more likely to struggle with mental health. Yet more unlikely to seek help.
In male-dominant workplaces like manufacturing it’s trickier, so prepare for pushback.
Forward-thinking leaders in manufacturing realize that prevention is key.
June: Feedback Month
Let’s spread some positivism this month!
Use post-it notes where employees can leave fun encouraging messages to each other.
Print and hand out a fun habit tracker.
We made a pdf habit tracker for you here!
This way people can tick off each day. An easy way to remember to share some positive comments about fellow coworkers.
There’s enough negativism going on. Let’s focus on the good.
If you’re measuring the impact of your leadership actions with the Celpax device, get line managers to use the daily huddles to spread the message.
Next, verify the impact in the leadership data.
Is the mood higher this month?
July: Meet our customers
A while back Matt Kanz, Director Of Continuous Improvement, gave a keynote at the Manufacturers Alliance.
Matt gave an interesting example of the power of hands-on contact with customers.
In his previous position as a Plant Manager, one of his employees forgot to include a parcel. When pointing it out, a shrug showed how little concern his coworker had given to the impact this would have on their customer.
So Matt invited his colleague into his office.
Probably expecting to be told off, the guy sat down. Next thing, Matt called the client to explain that the product wouldn’t arrive on time as expected. He apologized, without mentioning the specifics or who was to blame.
Over the speakerphone, the employee could hear firsthand how the client reacted. He learned how his action directly impacted the person on the other side of the line and his business.
To sum up, the client was not pleased.
At all.
This employee went on to be one of the most trustworthy and hardworking people Matt ever worked with.
But stepping closer to the business reality and your customers shouldn’t be a thing that happens just when something goes wrong.
Get sales and marketing involved to share their customer understanding reports. Invite customer service to share some stories from their day-to-day interactions. Storytelling is certainly highly effective.
Some easy suggestions for your customer month:
- Give away swags from your customers
- Send a handwritten note
- Get shop floor workers to go out a day on the trucks to deliver
- Invite customers for a picnic outside the manufacturing site
- Showcase customer success on screens
- Win a prize from customers
- Invite customers to “walk a mile in my shoes” and experience the shop floor, guided by your employees only
- Get shop floor employees to call customers to see how they’re doing
August: Ice cream Tuesdays
Summer shutdowns, holidays… August in Europe is traditionally a slow month.
It’s time to relax a bit. Give yourself a pat on your shoulder for a job done so far!
Then call a local ice cream provider. Have them park their van outside your manufacturing facility each Tuesday!
Your manufacturing site might still be open at full steam. Or you’re performing maintenance work or upgrades.
For those still showing up for work in August, cold ice cream is always a nice gesture.
It’s also a nice chance for management to have an informal chat and perhaps get some insights.
To sum up, small things can go a long way when it comes to leadership.
September: Listening
As your coworkers are back (hopefully relaxed?) after their holidays, it’s time to focus on the skills of listening.
What systems do you have in place to find out, and write down, the issues that your people find in their day-to-day?
Visualizing using Team Boards is a great way to get your people to suggest process improvements and bring forward ideas. In addition, you can easily keep people updated on progress.
Thomas Schlätzer is the Managing Director at German rope manufacturer Gleistein. He has a straightforward approach to employee suggestions.
A Celpax user since 2019, a whopping 80% of their improvements last year came from their employees:
“We have Just-Do-It-boards all over the place, located at our Team Boards”, he says.
“It follows the principle of PDCA (plan–do–check–adjust). 1-3 times per week, the team leader and the next level manager come together to discuss the suggested topic or problem.”
“If something isn’t clear the employee joins the discussion to describe the problem. He or she is also asked about what would be helpful. We also ask if perhaps he or she can find the solution himself, or do the improvement, or has proposals. Then it is immediately decided if the task is to be followed up or if is shelved. If accepted, then the next step or measure is taken straight away.”
“Our experience is extremely positive”, Thomas continues.
Established in 1824, Gleistein has solved everything from minor small solutions to more complex solutions using this method.
“So far we’ve probably had about 500 ideas, where probably 95% have been accepted and followed up. At least 85% of that 95% is already solved.”
And this is when it gets interesting, as Thomas sees the intensity going down as the problems become less and less obvious in the business.
“We’ll see how it develops. One thing is sure: it’s an incredibly good and easy measure. Much better than any big “improvement process-procedure”, he concludes.
Above all, it’s a cool way for leaders in manufacturing to create a problem-solving mentality.
Would you try it at your company?
Related: What is Six Sigma?
October: Manufacturing Month
Celebrate Manufacturing Month together with your team!
Let’s put a spotlight on those who manufacture goods and feel pride about our industry and profession.
Showcase your plant to potential new workers, and spread some good vibes.
Ideas for your company:
- Open Day at your manufacturing facility
- Manufacturing Trivia Quiz
- Go explore another manufacturing site in your area
- Send your people to talk at a local school or university
- Get staff to share why they started in manufacturing and what they like about it
- #ManufacturingMeal on October 1st to celebrate Manufacturing Day
- Workshops: What new products would shop floor workers go for?
- Family Day
It’s also a great opportunity to put a spotlight on diversity and inclusion among your team.
In other words, having female leaders in manufacturing positions might inspire more women to want to join your business.
Industry Week shares some tips here.
November: Quality
November 11th is World Quality Day.
The event happens every second Thursday in November. Many leaders in manufacturing use this day as a nice reason to celebrate the company’s achievements so far.
If your goal is safety at work, arrange a party to celebrate X amount of days without a Lost Time Accident (LTA).
For example, check out the yummy cake from the celebration at the manufacturing site at Syncreon.
Need ideas?
Firstly, you could put a “Quality Question of the Week” on your Team Boards.
Rally up your upper management, VPs, sales managers, finance, etc.
Get them to ask operators to answer a question or two. (Avoid direct line managers asking their people.)
If they know the question, award them! How about 20-minutes of flex time?
Or a healthy snack, swag, or something that resonates with your people.
Tie it back with the customer month. Take a moment to appreciate the customer value you’ve created so far through your efforts.
Also, get your operators to explain the quality measures you take when customers come to visit.
Secondly, organize a fun Quality Treasure Hunt!
- Leave something in every area/dept that is off or shouldn’t be there.
- Make it relevant. What drives you nuts when not done properly? Or what frequent errors cause quality issues? Don’t be afraid to geek out! Make sure it’s something that wouldn’t impact production.
- It could be using an old version of a control document, something which is marked in the wrong way (or unmarked)…
- After that, get your team to search the area to find out what it is.
- Consequently, award with something fun or unexpected. Or give them X amount of cash that they can choose how to spend together as a group. Just don’t complain when they leave cake trails on the control chart
December: Learnings & Planning
December is typically a busy month for most companies.
Carve out some time for line managers to wrap up the year together with their teams. Perhaps over gingerbread cookies?
Successful leaders in manufacturing look at the whole picture:
What has worked well in our business?
After that, let’s look forward: What should we start, stop and continue doing next year?
If you print the calendar with the monthly themes, you can revise the impact of each month together.
And if you’re measuring employee morale progress with the Celpax device, print the yearly graph with the trend line.
Firstly, how did you do compared to last year? Secondly, which events had the biggest impact on your team?
Above all, celebrate in style!
Get employee feedback with one powerful question.
Measure the impact of your leadership activities:
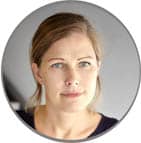